Burr in Casting: Enhancing Quality and Precision
Burrs are little, jagged edges or metal fragments that protrude from a cast after it has been molded. They frequently leave rough patches around the edges once the metal cools and hardens. Despite their apparent modest size, burrs can pose issues by making parts dangerous to handle or difficult to fit.
In the casting process, burr removal is an essential step. Without it, the finished product may not function as safely or smoothly as it ought to. Manufacturers may guarantee that the parts are safe, usable, and functioning by meticulously smoothing off these rough areas.
1. Understanding Burrs in Casting: What They Are and How They Form
After the metal has cooled and set in the mold, burrs—unwanted protrusions or rough edges—appear on the casting. They typically happen at the locations where the component was cut or taken out of the mold, or where the molten metal meets the mold surface. These flaws can range in size from small, nearly undetectable nicks to bigger, more noticeable metal extensions. Burrs are essentially a byproduct of the casting process that arises from defects in the mold design or excessive material flow.
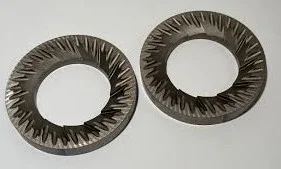
Burrs will almost certainly occur, particularly in complicated or high-precision castings. When molten metal is poured into a mold, the quick cooling process may result in a hardening effect that causes the metal to cool unevenly, leaving jagged edges. Burrs can also be produced by places that experience too much pressure or friction during molding, particularly around corners or holes. Although these little flaws are inevitable in metalworking, they must be fixed to guarantee the end product’s quality.
In some circumstances, burrs may also develop as the casting separates from the mold, particularly if any casting-related residue remains. Regardless of their size, these burrs must be found quickly. Post-casting cleanup is a required step in many sectors since, if left unchecked, they can damage the cast part’s functionality and safety.
2. The Impact of Burrs on Casting Quality
Burrs must be removed to ensure smooth operation and structural integrity because they can impair the final cast part’s performance. Burrs can disrupt the assembly process by obstructing tight component fits when they are left on a part. Burrs around holes or edges, for example, might make it more difficult to insert bolts, screws, or other fastening components, requiring more rework and causing production delays.
Burrs are a real problem from a safety standpoint. Workers who handle the parts may sustain cuts or abrasions from these sharp edges, and they may even develop stress points that cause the parts to crack or break under pressure. Even the slightest burr can result in serious performance or safety problems in sectors where accuracy and safety are crucial, such as the manufacturing of medical devices, automobiles, or airplanes.
Burrs can also negatively impact a cast part’s final look from an aesthetic standpoint. Burrs can produce a less polished, less professional finish in fields where aesthetic appeal is crucial, including consumer goods or design-driven initiatives. This may damage the manufacturer’s reputation and result in unhappy customers and product returns.
3. Methods for Removing Burrs in Casting
Deburring, the process of eliminating burrs, is necessary to produce a cast part that is safe, clean, and functional. Different casting kinds and production quantities are best suited for different deburring techniques. One of the most popular techniques is mechanical deburring, which physically removes burrs from the surface using instruments like brushes, grinders, or abrasive wheels. This method may be completed fast and effectively in large production situations and is effective for moderate burrs.
Manual deburring may be required for pieces that are more complicated or fragile. Expert craftsmen meticulously smooth the edges and remove any burrs without causing any damage to the part itself using hand tools like files, knives, or sandpaper.This technique is frequently employed when automated procedures might be too harsh or for small quantities of intricate items that demand a greater level of precision.
Manufacturers may use chemical or electrochemical deburring in specific situations. These methods dissolve or eliminate burrs without causing any harm to the casting by using certain liquids or electrical currents. While electrochemical deburring offers a precise and controlled method of burr removal, it is especially helpful for hardened or hard-to-reach burrs. Chemical deburring can be quite successful for intricate parts with complex geometries.
4. The Role of Quality Control in Burr Detection
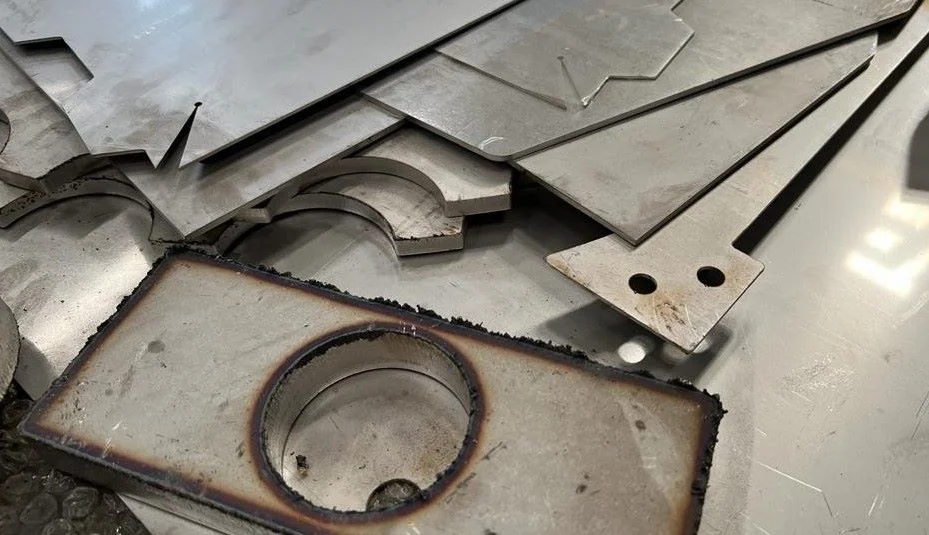
Quality control (QC) is essential in the casting industry for detecting burrs and making sure they are appropriately fixed. The simplest QC technique is visual inspection, in which skilled workers check castings for any obvious burrs or sharp edges. This method can overlook smaller, more subtle flaws, but it frequently works well for larger burrs. For this reason, a lot of businesses use sophisticated inspection technologies that can find burrs that are invisible to the human eye, such 3D scanning or ultrasonic testing.
Measuring the burrs’ size and placement to determine how they affect the part’s operation is another crucial component of burr detection. The fit or strength of the part could be impacted by even a tiny burr in high-precision industries. Accurate part measurements are made using digital equipment and laser measuring machines, guaranteeing that burrs are found and fixed before they proceed further down the production line. In manufacturing, these technologies aid in maintaining uniformity and high standards.
Lastly, some businesses use automated systems that can detect and remove burrs in a single, smooth operation. These technologies detect burrs and autonomously remove them using robots fitted with sensors or cameras. In high-volume manufacturing settings, where human inspection may not be able to keep up with the speed, automation is particularly advantageous. In addition to increasing accuracy, these methods lower labor expenses and human error.
5. Preventing Burrs: Design and Process Considerations
Although deburring is an essential step in the casting process, it is significantly more efficient to stop burrs from forming in the first place. Engineers can reduce the possibility of burr development by properly designing the mold and taking into account elements like flow dynamics and material shrinkage. Smoother castings from the beginning can result from, for instance, avoiding sharp edges and making sure that cooling is uniform.
Another important factor in lowering burr formation is material selection. Due to their brittleness or cooling properties, some metals or alloys may be more likely to generate burrs. Manufacturers can produce castings that are cleaner and more refined by using materials that are less inclined to develop sharp edges when cooled.Furthermore, casting methods like pressure die-casting, which entails forcing molten metal into a mold, can result in parts that are more precisely made and have fewer burrs.
Lastly, burr creation can be greatly influenced by the casting process itself. Manufacturers can lessen the likelihood of burrs forming by fine-tuning the mold’s general design, modifying cooling speeds, and optimizing pouring temperatures. By investing in cutting-edge technology, such as vacuum-assisted techniques or controlled atmosphere casting, the casting environment may be better regulated, resulting in parts that are smoother and more precise right from the start.